Anyone that’s spent time in the Logan Square neighborhood is surely familiar with the Cresswell Iron Works building, even if they didn’t know anything about its history. Between 1885 and 1969, Cresswell operated out of a low rise building at 113 N. 23rd St., producing a variety of iron products, like columns, lintels, brackets, girders, stairways, castings for bridges, and manhole covers. Over the last fifty years or so, the building was chopped up into a few tenant spaces, occupied by various businesses and some artists as well. But the building was probably most commonly known for the thick coat of ivy on its facade.
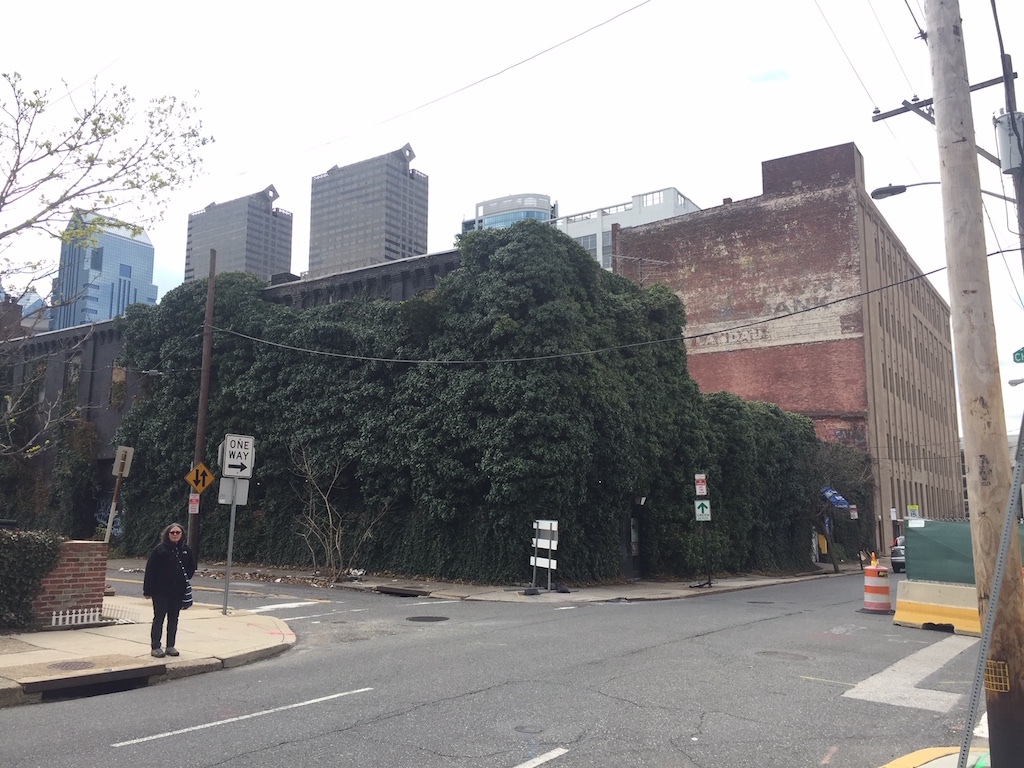
The property was on and off the market for years, but the asking price was too high to make redevelopment financially feasible. Last year, we shared the news that a developer finally found the right combination of acquisition price and project and that something would finally be happening here. At the time, we were a little shy on details, but we did tell you that old structure would be torn down and a 16-unit project would replace it. Today, we have pretty much all the details, and can show you that the project has moved along quite well since our initial post about the property.
US Construction is the developer, marking yet another Logan Square foray for the company that built townhomes on the former site of the Please Touch Museum. Similar to that project, the 23 Logan development will include high end homes, with all the bells and whistles you expect when the prices start at $1.8M. The homes will include elevators, 3-car parking, high end appliances, smart home features, and so on. Cecil Baker did the design work, and the renderings show contemporary exterior designs.
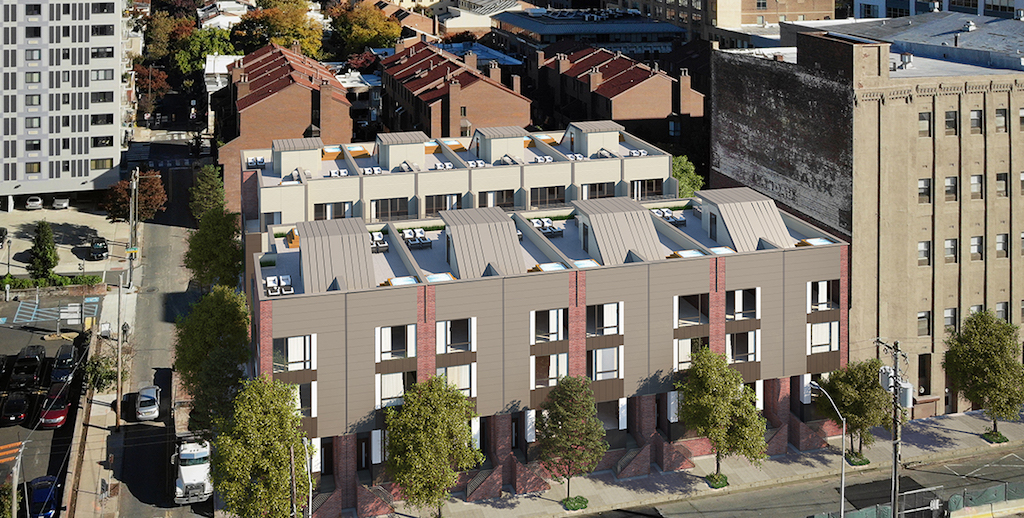
When we visited the site, we noticed that the homes are being fabricated offsite by a company called Blueprint Robotics. The approach here is similar to modular projects we’ve covered previously, but with some notable differences. Modular companies typically construct “pods” in their factories, complete with plumbing, electrical, ductwork, drywall, tile work, and so forth. Those pods get stacked onsite, tied together, and viola, you’ve got yourself a building. The Blueprint method is to fabricate everything offsite, but to assemble it onsite, leaving all the finish work to the builder. We couldn’t tell you which approach is more cost effective, but we do know that traditional modular construction isn’t really feasible on lots wider than 16′, as the pods get too wide to fit down city streets. So for this project at least, traditional modular methods wouldn’t have been an option.
We can’t say the same for the huge project that’s currently under construction across the street. Remember, a couple of high rises with roughly 600 units are planned for this location, along with a supermarket. We’ve only seen modular projects go up maybe half a dozen stories in Philadelphia, but there are a few examples of modular buildings rising over 30 stories in other cities, including a 359-foot building in Brooklyn. So high-rise modular construction is definitely possible, even if we haven’t seen it around here. Certainly, we could see this construction method make inroads into high rise construction in Philadelphia in the future, but we would have to think that the unions wouldn’t appreciate the competition.